Produkcja zaawansowanych technologicznie stopów ołowiu odbywa się w kilku, ściśle ze sobą powiązanych etapach.
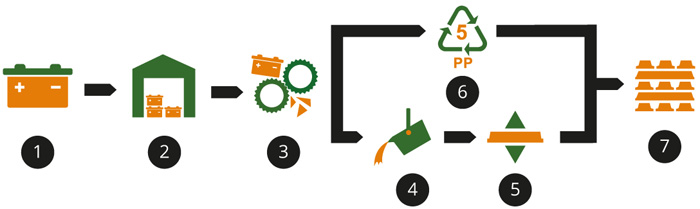
Pierwszym krokiem jest pozyskanie surowca. Dzięki działającej w całej Polsce sieci odbierającej zużyte akumulatory Orzeł Biały ma zapewniony dostęp do surowca. Aby w większym stopniu wykorzystywać moce produkcyjne zakładu, spółka regularnie importuje surowce uzupełniające. Zużyte akumulatory, jak wszystkie inne surowce będące odpadami niebezpiecznymi, są transportowane w specjalnych, szczelnych pojemnikach do zakładu w Piekarach Śląskich.
Wszystkie komponenty zużytych akumulatorów poddawane są recyklingowi.
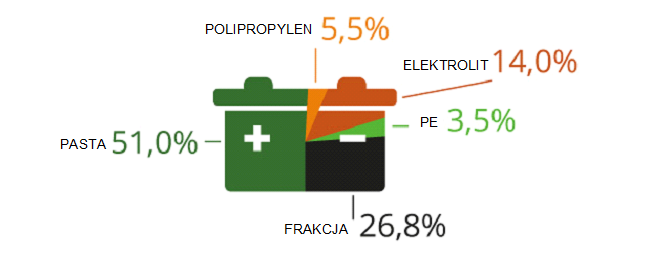
Po pozyskaniu i przetransportowaniu surowca rozpoczyna się właściwy proces produkcyjny, którego pierwszym etapem jest recykling zużytych akumulatorów ołowiowych, który obejmuje wydzielenie poszczególnych frakcji: elektrolitu, pastę ołowionośną, frakcję metaliczną i frakcję tworzyw sztucznych. Elektrolit jest neutralizowany, przetwarzany do postaci gipsu, a następnie składowany. Polipropylen po pokruszeniu i oczyszczeniu przerabiany jest na granulat i sprzedawany. Pasta ołowionośna i frakcja metaliczna trafiają natomiast do oddziału hutniczego, który jest kolejnym etapem procesu produkcyjnego.
W piecach hutniczych odbywa się proces przetopu frakcji metalicznej i pasty ołowiowej uzupełnionych o złom żelaza oraz sodę. Każdy z czterech pieców zainstalowanych w zakładach Orła Białego współpracuje z wysokosprawnym układem oczyszczania gazów technologicznych, co minimalizuje wpływ zakładu na środowisko.
Produktem przetopu jest ołów surowy, który w kolejnym etapie procesu trafia do rafinerii, gdzie w wyniku procesów rafinacji powstają wysokogatunkowe stopy ołowiu oraz ołów rafinowany. Dzięki automatycznej kontroli temperatury, w jakiej przebiega proces technologiczny Orzeł Biały gwarantuje wysoką jakość i powtarzalność produkowanych stopów.
Działalność produkcyjna w zakładach Orzeł Biały charakteryzuje się cyklem produkcyjnym, w którym odpady zostają przetworzone i zagospodarowane lub składowane.