The production of high-tech alloys takes place in several closely related stages.

The first step is to obtain the raw material. Owing to the country-wide operating network collecting used batteries, Orzeł Biały has a secured access to raw material. To make greater use of the production capacity of the factory, the Company regularly imports complementary raw material volumes. Waste batteries, like all other raw materials that are hazardous waste, are transported in special sealed containers to the treatment site at Piekary Śląskie.
All components of used batteries are recycled.
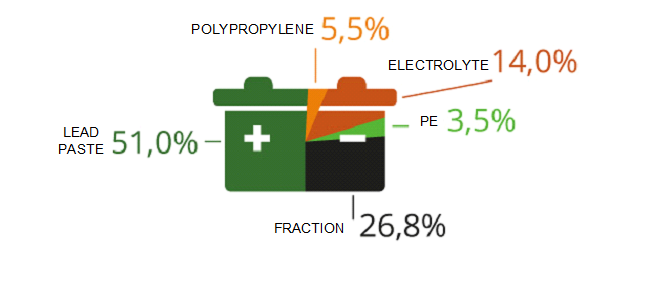
After collecting and transporting raw materials, the actual production process begins, the first stage being the recycling of used lead-acid batteries which includes the separation of different fractions: electrolyte, lead paste, metallic fraction and plastics fraction. The electrolyte is neutralised and then processed to form gypsum, and stored afterwards. Following crushing and purification, polypropylene is processed to granulate and marketed. Lead paste and metallic fraction are brought to the smelting site, which is the subsequent stage of the production process.
Smelting furnaces process metallic fraction and lead paste with added scrap iron and soda. Each of the four furnaces installed in plants of Orzeł Biały operates a highly efficient process gas cleaning system, thus minimising the environmental footprint of the factory.
The smelt product is crude lead which is brought in the next stage of the process to a refinery where, as a result of refining steps, high-grade lead alloys and refined lead arise. Thanks to an automatic temperature control of the processes at Orzeł Biały high quality and repeatability of produced alloys are guaranteed.
The manufacturing activities of Orzeł Biały facilities feature what is called a closed cycle which means that any waste is processed and re-used or stored.